The common problems and analysis of polycarboxylate superplasticizer in precast concrete include their low dosage, high water reduction rate, good plasticizing performance, strong compatibility with cement, and low concrete shrinkage. According to feedback from initial users, polycarboxylate superplasticizers are more convenient, safe, and efficient compared to previous generations of water reducers.
There are significant differences in molecular structure, mechanism of action, and performance in concrete between polycarboxylate water reducers and traditional water reducers. Therefore, understanding and using them correctly is crucial for promoting the application of polycarboxylate water reducers.
This article will focus on the following common problems that may arise during the application of polycarboxylate water reducers in precast concrete in construction projects, and provide analysis and solutions based on actual situations.
- Compatibility of polycarboxylate superplasticizers with cement
- Sensitivity of the dosage of polycarboxylate superplasticizer
- Excessive dosage of polycarboxylate-based high-efficiency water reducing agent leads to excessive air bubbles on the surface of concrete structures.
- Overdosing of polycarboxylate superplasticizer leads to prolonged setting time.
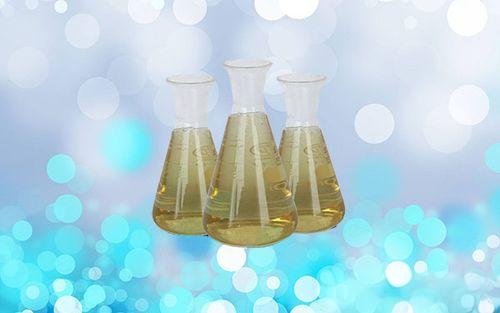
Compatibility of polycarboxylate superplasticizers with cement
Cement and cementitious materials have complex and varied compositions. Although polycarboxylate superplasticizers have a wider range of adaptability compared to naphthalene-based water reducers, they may still have poor compatibility with some types of cement. This is often reflected in a decrease in water reduction rate and an increase in slump loss.
How can we avoid delays in construction progress and potential losses caused by this issue?
It is essential to conduct adaptability tests on each batch of cement before use. Additionally, a compatibility test should be carried out using the construction mix ratio for each batch of cement before opening.
Sensitivity of the dosage of polycarboxylate superplasticizer
Due to the significant reduction in water consumption when using polycarboxylate superplasticizer, the water-cement ratio is typically between 0.3-0.4, and in some cases, even lower than 0.3. In such low water consumption situations, fluctuations in the amount of water added can result in significant changes in slump and may cause sudden increases in slump and bleeding in the concrete.
Phenomenon: The contract requires a slump of 150mm ± 30mm at the construction site. However, when the concrete is measured upon arrival, the slump is 180mm. After transportation to the construction site, the slump is measured at 210mm, resulting in two consecutive trucks of concrete being rejected and returned to the factory. Upon further testing, the slump is still measured at 210mm, and there is evidence of bleeding and segregation.
Reason: The cement used has good compatibility with the water reducer, and the dosage of the water reducer is slightly higher. The mixing time is not sufficient, and the measured slump upon discharge is not the true slump due to the short mixing time.
Prevention: For cements that are sensitive to the dosage of polycarboxylate superplasticizers, the dosage should be appropriate, and the measurement accuracy should be high. It is also recommended to extend the mixing time, even with a twin-shaft forced mixer, the mixing time should not be less than 40 seconds, preferably more than 60 seconds.
Excessive dosage of polycarboxylate-based high-efficiency water reducing agent leads to excessive air bubbles on the surface of concrete structures.
To enhance pumpability and durability, it's beneficial to increase the air-entraining agent appropriately since many polycarboxylate superplasticizers have significant air-entraining properties. Like naphthalene-based water reducers, polycarboxylate superplasticizers also have a saturation point. If the dosage of the admixture is near its saturation point, adjusting the amount of paste in the concrete mix or using other methods is necessary to improve the workability of the concrete mix.
Issue: A mixing station consistently used polycarboxylate superplasticizers to prepare concrete. Suddenly, one day, a construction site reported excessive air bubbles on the surface of shear walls after formwork removal, resulting in poor aesthetics.
Cause: On the day of pouring the concrete, the construction site repeatedly reported low slump and poor workability, prompting the laboratory personnel at the concrete mixing station to increase the dosage of the admixture. The site used large steel formwork, and too much material was poured at once, leading to uneven compaction.
Prevention: Strengthen communication with the construction site, strictly follow the specifications for pouring height and compaction methods. Adjust the amount of paste in the concrete mix or use other methods to enhance the workability of the concrete mix.
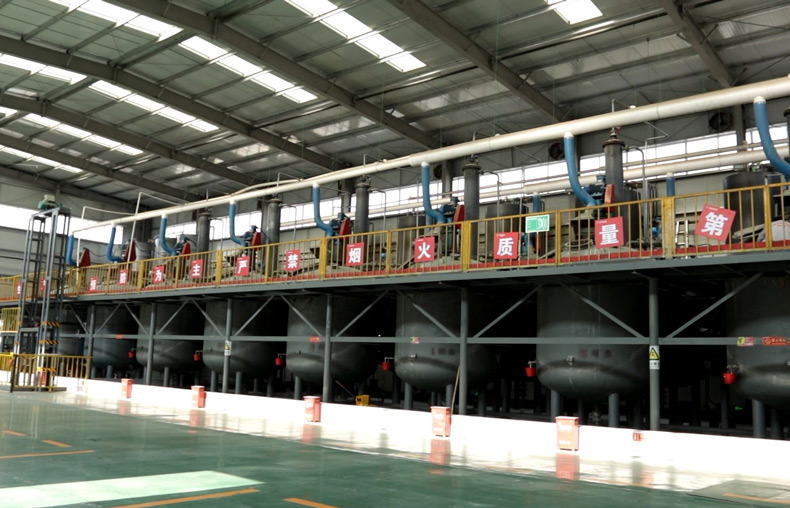
Overdosing of polycarboxylate superplasticizer leads to prolonged setting time.
Issue: Concrete has a high slump, and it takes 24 hours to finally set. After 15 hours of pouring structural beams and slabs at a construction site, some parts of the concrete were still not solidified. Upon inspection by engineers from the mixing station and subsequent heating treatment, it took 24 hours for the concrete to finally set.
Cause: Excessive dosage of the water reducer, combined with low nighttime temperatures, resulted in slow hydration of the concrete. Workers at the site added water to the concrete without authorization, increasing the water content.
Prevention: Adhere to appropriate dosage of admixtures with precise measurements. Remind workers to ensure proper insulation during lower temperatures and avoid adding water arbitrarily, as polycarboxylate-based admixtures are sensitive to water content.
polycarboxylate superplasticizers are high-performance admixtures with low dosage, high water reduction rates, and minimal slump loss. The variety of polycarboxylate water reducers available in the market differ in synthesis pathways, raw material sources, quality, and production processes, leading to variations in product performance. Continuous experimentation and evaluation are essential to understand the characteristics of polycarboxylate superplasticizers. Fuluorui, based on experimental foundations, continually optimizes the performance of polycarboxylate superplasticizers. The currently available polycarboxylate water reducers are highly acclaimed in the market.