The rapid loss of concrete slump caused by the addition of water-reducing agents significantly impacts the application and performance of concrete, especially with the thriving development of the commercial concrete industry in recent years. To address this issue, numerous scholars have conducted extensive research and reached consensus on several factors that affect the loss of concrete slump. These factors include cement composition, types of water-reducing agents, environmental temperature and humidity, mixing methods, water-cement ratio, timing of water-reducing agent addition, and types of admixtures. All of these factors to varying degrees influence the slump loss of concrete. Among them, the primary factors are the composition of cement, the type of water-reducing agents, and the timing of water-reducing agent addition.
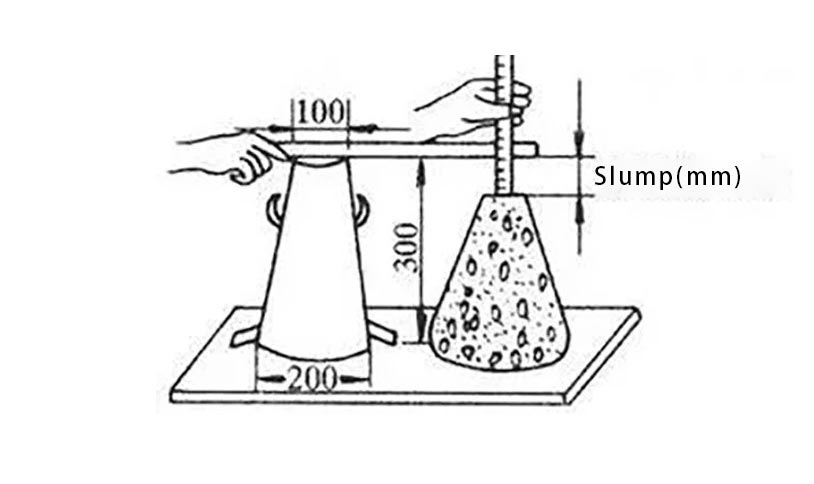
The mineral components in cement are the primary factors influencing the loss of concrete slump. Many scholars have conducted adsorption experiments using individual minerals in cement with a certain concentration of water-reducing agents. The results indicate that the minerals in cement, including C3A, C4AF, C2S, and C3S, exhibit selective adsorption of water-reducing agents. When the concentration of water-reducing agent is 0.4%, in the absence of gypsum, the adsorption capacities are as follows: C3A at 150mg/g, C4AF at 280mg/g, C3S at 22mg/g, and C2S at 1.9mg/g. In the presence of gypsum, the adsorption capacities are: C3A at 15mg/g and C4AF at 40mg/g. From the results of these experiments, it is evident that due to the significant adsorption of water-reducing agents by C3A and C4AF, the minerals C3S and C2S, which constitute a larger portion of cement composition, have insufficient adsorption capacity. As a result, the zeta potential decreases significantly, leading to a substantial loss of concrete slump. Water-reducing agents cause the concrete slump to decrease due to this fundamental reason.
In view of the above reasons, people have carried out extensive and in-depth research. Up to now, it is considered that the following methods are effective to inhibit the slump loss of water-reducing agent concrete:
1、The stagnant water mixing method and post-addition method:
The so-called stagnant water mixing method and post-addition method refer to the practice of adding a water-reducing agent after the mixing of sand, gravel, cement, and water (partially or completely). This method has a significant effect on reducing the loss of concrete slump caused by the addition of water-reducing agents.
The primary cause lies in the rapid generation of C3AH8 and C4AFH10 when cement reacts with water due to the presence of C3A and C4AF. In the presence of gypsum, AFm becomes the primary product, leading to a substantial decrease in the levels of C3A and C4AF within the system. Consequently, the consumption of water-reducing agents by C3A and C4AF experiences a significant reduction. C3S and C2S can efficiently absorb a significant proportion of the water-reducing agent. This leads to a notable increase in the zeta potential of cement particles, maintaining a relatively steady zeta potential over a specific duration. Consequently, this directly enhances the workability of concrete and minimizes the extent of slump loss.
This approach is straightforward and readily applicable, enjoying extensive utilization within the concrete industry at present.However, there are certain limitations and restrictions in its effectiveness and application.
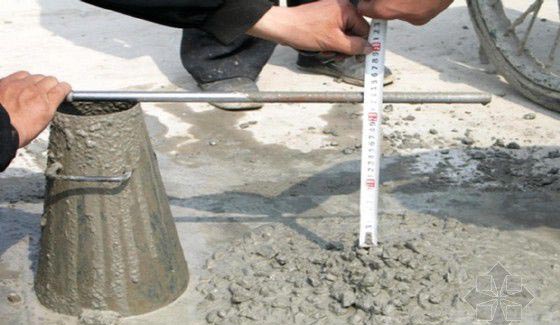
2、Admixture Method for Inhibiting Slump Loss
Numerous admixtures exist for counteracting the slump reduction in concrete attributed to water-reducing agents. These admixtures can be broadly classified into inorganic and organic types.Regardless of whether they are inorganic or organic, they all share a common characteristic of delaying the setting time of concrete to varying degrees.
Another type of admixture that suppresses slump loss belongs to the reactive category. Admixtures made from maleic anhydride and olefins copolymerization, as reported, continually release dispersants into the water-cement hydration system through chemical reactions when added to concrete. This action helps maintain a consistent zeta potential of cement particles, thereby achieving the purpose of inhibiting slump loss. This method represents a trend for future development.
It's important to highlight that recent years have seen extensive research conducted on polymers like acrylic acid and its salts, methyl acrylic acid and its salts, and acrylamide.The polar functional groups -COOH and -CONH2 in these polymers can form numerous ether bond derivatives, all of which exhibit excellent dispersing effects. Due to their differing dissolution rates compared to water-reducing agents (especially naphthalene sulfonate formaldehyde condensate), they can steadily provide water-reducing agents to the water-cement hydration system. As a result, the zeta potential of cement particles remains relatively stable within a certain time frame, effectively inhibiting slump loss. At present, this method is extensively utilized overseas and has yielded positive results. It should garner the attention of professionals in our country's admixture industry.
3、Granulation Method
The concept of the granulation method involves creating particles of different sizes and dissolution rates for water-reducing agents and their carriers. These particles are then mixed into freshly prepared concrete. This leads to the formation of varying dissolution gradients within the water-cement hydration system, allowing for the timely replenishment of water-reducing agents consumed by C3A and C4AF. This ensures that the system maintains water-reducing agents at a critical micelle or near-critical micelle state, thereby preventing or minimizing slump loss. However, the author has observed that many of the products in this category are less than ideal. Some have overly large particle sizes that become loose upon contact with water. Others have appropriate particle sizes but dissolve too quickly or too slowly, affecting their effectiveness.
According to the author's perspective, water-reducing agents should undergo a "coating" process during granulation. Ideally, this outer layer should dissolve gradually in an alkaline solution and possess varying thicknesses. This approach would enable the gradual release of the enclosed water-reducing agents over a defined timeframe, effectively preventing slump loss.The author has visited two manufacturing units producing such equipment and has had multiple discussions with them. One of these units employs a microcomputer-controlled granulation-coating machine. This equipment can produce spheres of various diameters as required and apply different thicknesses of coatings to them. The microcomputer governs the entire process. Currently, this equipment finds primary application in granulating spacecraft fuel, contributing to its relatively high price, which can pose affordability challenges for general units.
The other type is known as the DTP pressure spray granulation drying machine. It comes in a series of products with a maximum evaporation capacity ranging from 6 to 2000 kg/h and spray pressures from 2.6 to 2.5 MPa. Heat sources can include coal, electricity, natural gas, oil, etc. It can perform coating, but manual control is required. According to reports (though the author hasn't personally used it), this equipment performs well. It's cheaper than the previous type, but still costs tens of thousands to several hundred thousand yuan. Moreover, the pharmaceutical industry has numerous granulation and coating equipment, which can serve as references for adapting equipment to the needs of the admixture industry.
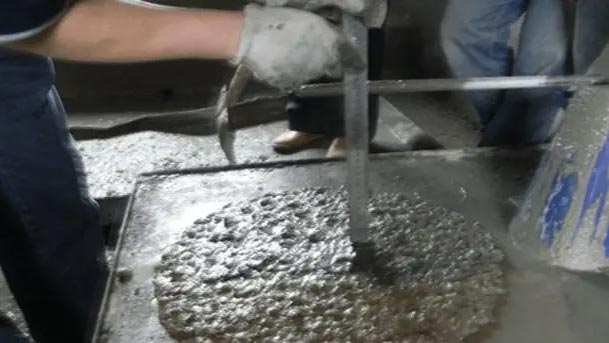
4、Concrete with lignosulfonate and molasses-based water-reducing agents experiences a smaller slump loss rate compared to concrete with naphthalene-based water-reducing agents.
The temperature of freshly mixed concrete significantly affects the slump loss. Generally, higher temperatures result in faster slump loss, while lower temperatures lead to slower slump loss. Testing various water-reducing agents at different temperatures (15°C, 25°C, 35°C) reveals that, on average, for every 10°C increase in temperature, the slump loss rate increases by 15-40% (due to variations in water-reducing agent types, the slump loss in concrete also varies). Therefore, during hot summer conditions, it is important for commercial concrete producers to address how to reduce the temperature of freshly mixed concrete. Mixing concrete with water from deep wells (which has a significantly lower temperature compared to surface water) effectively lowers the concrete temperature, thus benefiting the prevention of slump loss.
Additionally, if concrete needs to be transported over long distances during the summer, it is advisable to cover the concrete transport vehicles with insulating materials. This can have a significant impact, especially in areas where the metal surfaces exposed to sunlight can reach temperatures as high as 56°C.